What is Thermal Spraying? And why should you consider it?
Thermal spraying is a term that we use to describe our repair processes at New Metal surfaces. Thermal spray coatings are created by accelerating small particles of heated metal or ceramic towards the work surface so that it mechanically deforms and bonds resulting in a dense coating.
Currently at New Metal Surfaces, we offer our customers three thermal spray coating options:
SIGN UP
Enter your email to sign up to our newsletter!
Contact Us
Let’s take a deeper dive into what thermal spraying is, and why we believe you should consider it when looking at repairing your components.
THE BASICS
At New Metal Surfaces, when we say thermal spray coatings, we mean a coating that is produced by accelerating small particles of heated metal or ceramic towards the work surface (your component) so that it mechanically deforms and bonds resulting in a new coating. Essentially, a thermal spray coating is what we apply to your damaged or new components to restore or improve the surface of your component.
Through these coatings we can restore dimensional accuracy of metallic parts, and cost effectively improve some of your component’s characteristics, such as wear resistance, corrosion resistance, thermal conductivity and more. These improvements are made due to the selection of materials that we use in our thermal spray coatings, which can be altered dependent on the needs of your components.
There are a number of different terms that we use when describing thermal spray coatings, so let’s take a look at them.
BONDING & BOND STRENGTH
When we talk about a thermal spray coating bonding to the work surface, or we mention the bond strength of a coating, we are talking about how well the sprayed material and the work surface mechanically interlock and ‘stick’ together. The bond strength is the measure of the perpendicular force required (per unit area of coating) to pull the coating off the work surface.
There are many factors that affect the bond strength of a coating, these include:
- The blast depth and surface profile
- The velocity of the sprayed material
- The physical and chemical properties of the sprayed material
- The temperature of the sprayed material and the work surface
- The thermal spray process that is used
- Thickness of the coating
- The material deposition rate
- And much more…
At New Metal Surfaces we grit blast your components coating areas, because the rough surface profile that is produced from the grit blasting allows the sprayed material to better mechanically lock onto the work surface.
An advantage that our HVOF coatings have over the other processes we use for our thermal spray coatings is that the HVOF process produces coatings with higher bond strengths due to the high impact velocity that is achieved.
COATING THICKNESS
The thickness that can be achieved from a coating is dependent on the bond strength that can be achieved. For example, as more coating is deposited on a work surface, the residual stress in the coating is increases, once it reaches a point where that stress in more than that of the bond strength, the coating will fail. This is why we only spray certain thicknesses for certain materials – If we were to spray a material onto a work surface above that recommended thickness, we cannot guarantee that the coating will not fail.
Once again, another advantage of HVOF coatings is that we are able to produce low stress coatings that are extremely dense, and therefore more durable, in some cased, than other thermal spray processes that are offered by New Metal Surfaces.
POROSITY
When we mention that our HVOF coatings achieve little porosity, we are referring to the lack of pores or voids within that coating. Depending on the application of your component, porosity will be a detrimental or an important factor. Our HVOF coatings can achieve deposits with less than 1% porosity.
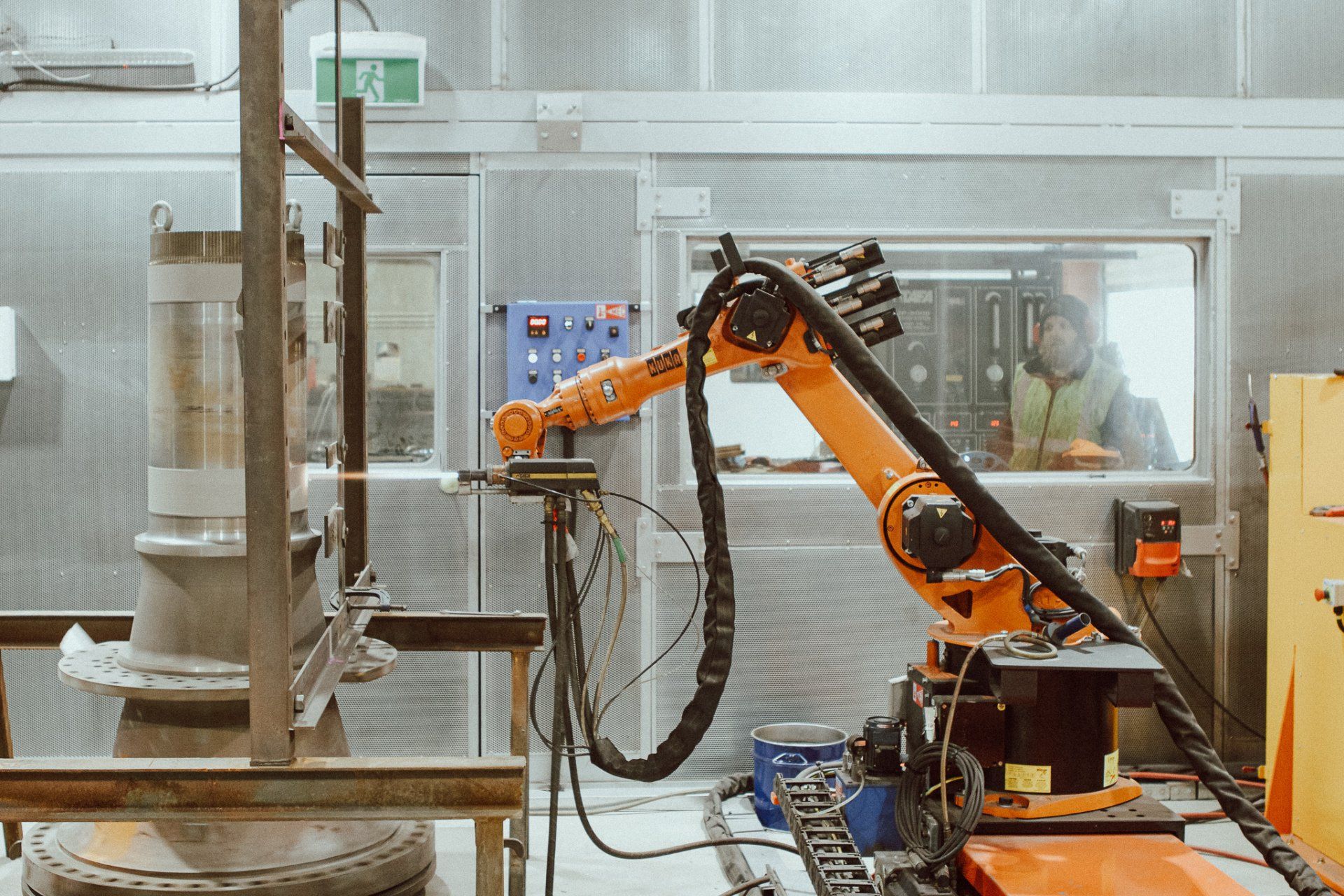
COATING PROPERTIES
At New Metal Surfaces we work with our customers to determine the best coating for their specific component needs, this allows us to produce a coating that has the properties that matter to you. For example, different choices in sprayed materials can produce coatings that have very different properties to each other.
Some of the properties that can be achieved by thermal spray coatings are:
- Increased wear resistance
- Increased corrosion resistance
- Increased heat resistance
- Increased electrical conductivity, or resistivity
- Increased abrasion resistance
Depending on the application of your component, we can tailor a coating that will allow it to perform more efficiently, and for longer periods of time – saving you money on continual replacements.
WHY YOU SHOULD CONSIDER THERMAL SPRAY COATINGS
We hope that the article that you have just read gives you a basic understanding of the different factors and elements to consider when choosing a thermal spray coating. Whilst some of these terms or processes might seem complicated (because they are), you can rest assured that our team knows what we are doing, and that your components would be safe in our hands.
By choosing a thermal spray coating, we will be able to work with you to enhance your component for your specific application. So, if you have a component that is in frequent need of repair or replacement, or if you want to improve the efficiency of your machinery, get in contact with us today to see how your business could be improved using thermal spray coatings.
WE'RE READY
Get in touch with us today to see how we can assist you with your thermal spray coating needs.